Как эффективно их объединить — кейс автозавода в Нижнем Новгороде
Современные экономические условия задают российской промышленности два важных вектора для развития на ближайшие 5-10 лет. С одной стороны, для повышения производственной эффективности и конкурентоспособности, всем предстоит перестроиться на высокотехнологичные рельсы, причем делать это нужно быстро и системно. А с другой, в контексте нехватки персонала, на первый план выходит продуманная HR-политика: одной зарплатой людей уже не удержать. Лидеры отраслей начинали этот путь еще в начале 2000-х и уже сформировали успешные практики.
В центре деловых повесток всех главных экономических форумов страны — от состоявшихся в июне нижегородского ЦИПРа и Петербургского международного экономического форума до грядущего уральского «Иннопрома» — по сути, два глобальных аспекта развития промышленности. Во-первых, на сессиях обсуждают условия для цифровой трансформации и за счет нее — роста производительности труда: как технологии влияют на эффективность бизнес-процессов, что нужно для успешной адаптации новых решений и какие из них действительно работают в российской реальности. А во-вторых, в фокусе внимания участников дискуссий — проблема дефицита кадров: как его компенсировать, чем усилить бренд работодателя и как грамотно выстроить баланс между инвестициями в технологии и развитием персонала.
Казалось бы, все эти вопросы не новы, но сегодня, в силу ряда внешних и внутренних причин, искать ответы приходится каждому собственнику и руководителю, вне зависимости от специфики и масштаба бизнеса — иначе не сохранить конкурентоспособность. Но лидеры отраслей — на то и лидеры, чтобы задавать тренды и «прокладывать лыжню».
Автозавод в Нижнем Новгороде сегодня продолжает удерживать порядка половины рынка в своем сегменте легких коммерческих грузовиков (LCV), причем четверть всего объема продаж таких машин в стране, по подсчетам отраслевого агентства «Автостат», приходится на «Газель Next». Позиции производителя сильны и стабильны на протяжении, без преувеличения, последнего десятилетия: кризисы сменяют друг друга, спрос то растет, то падает, на смену европейским брендам, которые еще совсем недавно вольготно чувствовали себя в условиях открытого российского рынка, пришли китайские… Но нижегородский автозавод продолжает укреплять репутацию производителя главных «рабочих лошадок» отечественного бизнеса и регулярно пополняет продуктовую линейку современными моделями.
Как ему это удается? Ответ стоит искать в начале 2000-х: именно тогда с подачи Олега Дерипаски те самые, так активно обсуждаемые сегодня, векторы на производственную эффективность и развитие людей стали для автозавода главными, определяющими развитие на годы вперед в любом контексте.
Производственная эффективность
Возвращаясь к дискуссиям на полях федеральных форумов, позволим себе еще одно обобщение. По сути, реалии и регуляторы ждут от отечественных производителей сегодня «российского экономического чуда». Аналогия понятна: в 1950-х настоящий прорыв в экономике совершили японские предприятия, и их опыт для нас в текущей ситуации актуален, как никогда. Многие, действительно, посмотрели на Восток и его подходы другими глазами: «бережливое производство», основанное на принципах производственной системы Toyota, стало одним из самых распространенных подходов к выстраиванию бизнес-процессов в отечественной промышленности.
В начале 2000-х Олег Дерипаска впервые привез японских консультантов на автозавод в Нижнем Новгороде. Позднее он объяснял, что в японском подходе его привлекла академичность: «Научность подхода — самое привлекательное для меня в этой системе менеджмента. Потому что, как и любую науку, ее можно упорным трудом постичь, развить, тиражировать, ее логике подчинять работу каждого звена нашего производства. Как и любой научный метод, его можно творчески развивать и совершенствовать».
Мыслить творчески, постоянно ставить вопросы и находить ответы — главное, чему учились у японцев, вспоминает директор по производственной системе автозавода Оксана Исакова: «Было понятно, что в российских условиях невозможно просто взять и повторить алгоритмы из методички и надеться на то, что это сработает. В краткосрочной перспективе — возможно, но для стабильного долгосрочного результата нужна система. Поэтому мы шаг за шагом строили собственную производственную систему, шли от одного участка к другому: анализировали, выявляли потери, стандартизировали работу — превращали качество в процесс шаг за шагом и таким образом меняли подходы, мышление сотрудников».
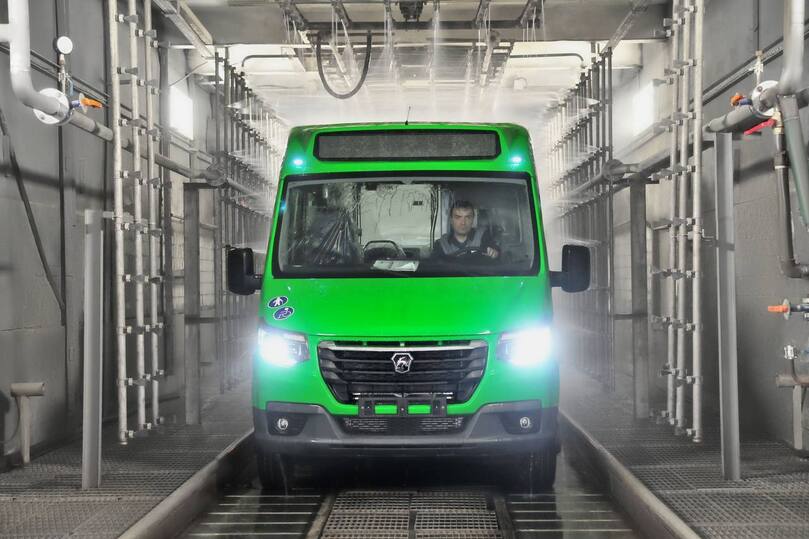
Сегодня принципы производственной системы охватывают все бизнес-процессы на автозаводе, от закупок и работы с поставщиками до логистики, продаж и сервиса. Она стала для предприятия новой философией, которая позволяет гибко реагировать на требования покупателей и постоянно развиваться.
Вся масштабная модернизация производства, которая продолжается на автозаводе на протяжении последних двух десятилетий, и текущая цифровизация тоже проходят по принципам производственной системы: каждый новой станок, новый робот и новое ИТ-решение вписываются в процессы, если в этом есть необходимость и очевидна эффективность. «Решения об автоматизации процессов всегда основаны на нескольких факторах: во-первых, они принимаются в силу экономической целесообразности, во-вторых, — когда требуется обеспечить высокую точность работ, и, в-третьих, — когда нужно изменить условия труда», — объясняет директор автозавода Андрей Софонов.
Именно так, например, несколько лет назад инженеры предприятия разработали специальные беспилотные платформы, которые помогли оптимизировать логистику внутри сборочных цехов и восполнить нехватку персонала. Сегодня эти грузовые платформы работают на 41 маршруте, перевозят 550 видов деталей. «А потом, благодаря привычке непрерывно совершенствовать любую операцию, возникла идея — а почему бы не использовать их собственно на конвейере? Сделали специальную надстройку, и роботы-беспилотники заменили сборочный конвейер мостов для „Газелей Next“. Это позволило обеспечить гибкость производственного процесса и повысить производительность», — рассказывает Андрей Софонов.
А современные цифровые решения помогают быстрее и точнее собирать аналитику — данные, которые, собственно, и обеспечивают непрерывность улучшений — один из главных принципов производственной системы. В 2023 году нижегородский автозавод выиграл грант Российского фонда развития информационных технологий (РФРИТ) и начал внедрять цифровой проект комплексного управления жизненным циклом продукта и технологическими процессами. Его суть в том, что специальные датчики, установленные на станках, в режиме онлайн снимают и загружают в систему всю информацию о них: сколько работают, сколько и по каким причинам простаивают, меняются ли показатели в зависимости от смены. В итоге эффективность загрузки оборудования выросла на 15%, общая экономия достигла 108 млн руб.
Корпоративная культура
Если считать производственную систему научным течением, то неизбежное следствие — появление приверженцев и последователей. По инициативе Олега Дерипаски нижегородский автозавод начал работать над воспитанием нового поколения сотрудников одновременно с повышением производственной эффективности. Конечно, традиции подготовки кадров на предприятии с уже почти вековой историей были и до этого. Но на современном этапе завод создал новые формы взаимодействия с местными школами, техникумами и вузами, чтобы готовить будущие кадры для новых задач автопрома.
Именно в Нижнем появились одни из первых в стране кружков робототехники, а студенты и преподаватели ведущих технических вузов страны начали на равных с конструкторами автозавода работать над созданием беспилотного автомобиля, машин на электротяге и водородном топливе и другими самыми современными технологиями. Постигать принципы производственной системы, а заодно — получать все необходимые здесь и сейчас компетенции, от наладки нового оборудования до углубленного изучения иностранных языков, сотрудникам помогает свой корпоративный университет — Академия современных технологий автомобилестроения, названная в честь Александра Николаевича Моисеева, стоявшего у истоков создания производственной системы автозавода.
А недавно, когда возникла острая необходимость в подготовке собственных цифровых инженеров, у автозавода появилась своя ИТ-академия, где студенты учатся на реальных производственных кейсах параллельно с основным курсом в вузе и по окончании уже работают в штате автозавода. «Мы погружаем ребят не только в особенности производственных процессов, ставя перед ними реальные задачи, но и в нашу корпоративную культуру, а это всегда драйв, чувство плеча и команды, будь то научная конференция, где молодые специалисты представляют свои смелые идеи под руководством наставников, лыжная гонка на корпоративной базе или волонтерство. В этом и заключается успешная адаптация новичков — то, что позволяет мотивировать и удерживать новое поколение сотрудников, для которых важна не только зарплата, но и причастность к большому общему делу», — рассказывает директор по персоналу автозавода Елена Марштупа.
Сам Олег Дерипаска, выступая на сессии ПМЭФ о новых источниках роста в мировой экономике, назвал науку и молодых специалистов главным конкурентным преимуществом страны. По мнению промышленника, именно современные выпускники физтехов и мехматов, а не ресурсы и господдержка, помогут России справиться с вызовами в технологической сфере. «Да, сейчас их (выпускников технических вузов — ред.) разбирают банки, IT-компании, это нормально. Но человек, который прошел хотя бы три тома Ландау, который прошел дифуры, никогда это не забудет. Эти люди способны разобраться, и они помогут нам решить практически любые проблемы. Я не вижу ни одной нерешаемой задачи, которая стоит перед нами в ближайшее время», — заключил Дерипаска. Опыт нижегородского автозавода показывает, что эта ставка на людей — самая перспективная.