С раннего утра, вместе с запуском производственных линий на Нижегородском автозаводе, приступают к работе специалисты службы качества. Они ведут скрупулезную оценку всех процессов, и только с их одобрительным штампом «ОК» в маршрутно-контрольной карте будущий автомобиль отправляется на следующий этап производства.
Приемка со стороны контролеров службы качества осуществляется на стадии сварки, окраски и сборки автомобиля согласно стандарта пошагового выполнения контрольных операций.
В цехах сварочно-кузовного производства проверяется соответствие комплектации кузова или кабины, соответствие зазоров, перепадов навесных деталей, а также качество лицевых деталей. Далее при помощи спецоборудования по чек-листу в световом тоннеле на кузове проверяются критические сварные соединения. На контрольно-измерительных приспособлениях тщательно анализируется геометрия кузовов, кабин и навесных деталей, которые должны соответствовать параметрам, заложенным в конструкторской документации.
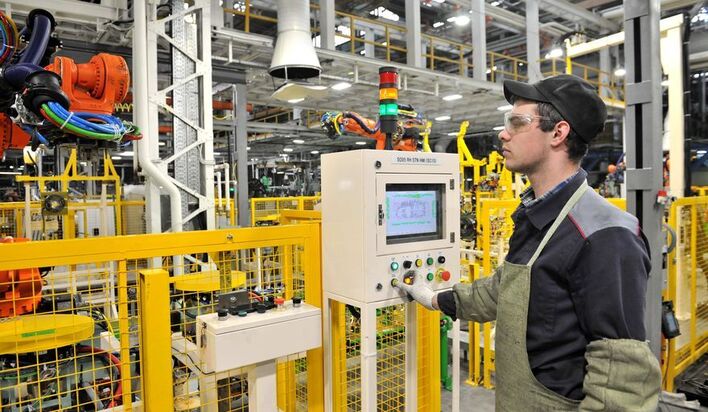
Для подтверждения надежности и качества сварных соединений кузова выборочно отправляют в созданную недавно лабораторию разрушающего контроля, оснащенную современным оборудованием. Там специалисты могут оценить не только длину шва и расстояние между сварными точками, но и самый важный параметр – так называемый диаметр ядра, который характеризует прочность соединения. Если есть несоответствие, достаточно откорректировать режим работы сварочной машины. Новая лаборатория стала поставщиком уникальных данных, которые позволяют сделать автомобиль лучше.
- По результатам проверки формируется отчет, где фиксируются все замечания, которые оперативно устраняются, - рассказывает начальник управления качества производства автозавода Евгений Лукьянов, работающий в службе качества нашего предприятия более 25 лет.
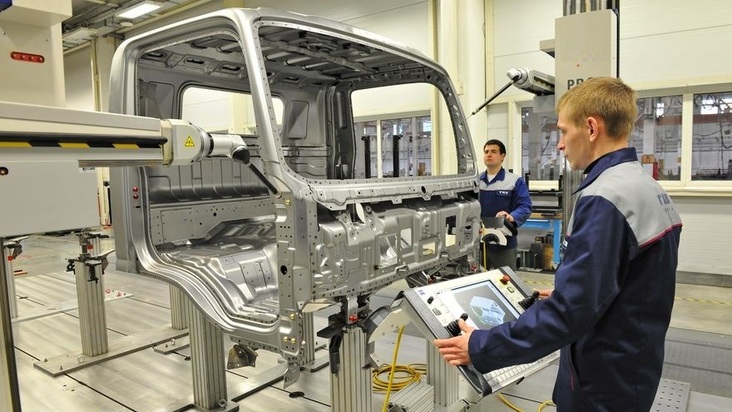
Далее по процессу, сваренный и собранный кузов или кабина, прошедшие контроль качества, отправляются на окраску. Причем, все лакокрасочные материалы предварительно проверяются в специальной лаборатории.
Пройдя все этапы подготовки и нанесения лакокрасочного покрытия, кузов или кабина поступают на станцию контроля качества. Здесь контролеры, визуально-тактильно проверяют качество лакокрасочного покрытия кузова, капота, дверей, боковин, крыши. Вооружившись специальными высокоточными инструментами, замеряют толщину лакокрасочного покрытия, его адгезию (сцепление с материалом подложки) и структуру. Анализируется и цветовая сходимость. Для этого используется высокотехнологичный прибор - спектрофотометр. Все эти мероприятия обеспечивают качественное лакокрасочное покрытие, что повышает удовлетворенность потребителя нашей продукцией.
- Все оборудование, которое используют в своей работе контролеры службы качества, соответствует современным стандартам автомобилестроения и применяется на ведущих предприятиях мира, - отмечает Е.Лукьянов.
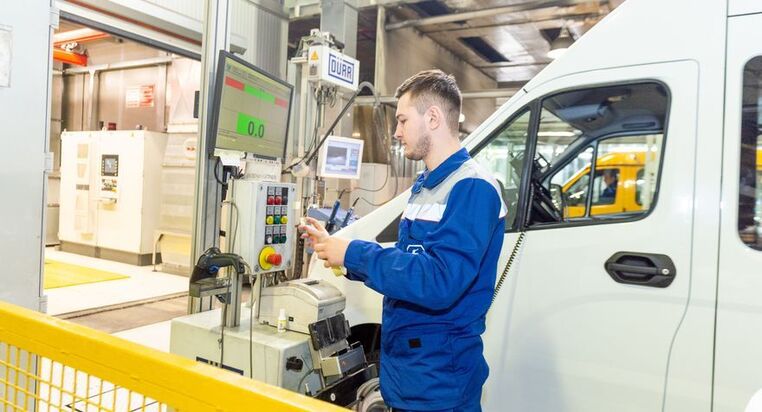
Передовые технологии в оценке качества продукции применяются и на сборочных конвейерах. Станции контроля здесь располагаются на всех основных участках. Первая приемка проводится на этапе сборки шасси автомобиля в перевернутом виде: контролируется прокладка трубок тормозной, топливной системы, электропроводки, крепление мостов, подвесок. После проверки оформляется контрольный лист качества сборки шасси. Поставленный в нем штамп «ОК» служит зеленым светом для переворота рамы. Окончательно собранная рама, полностью готовая для дальнейшего крепления кузова или кабины, также проходит тщательную проверку на качество и соответствие конструкторской документации.
Особое значение на главных сборочных конвейерах ПГА уделяется контролю качества выполнения критических операций (QCOS). Специалисты управления качества производства по маршрутному листу с помощью электронных динамометрических ключей проверяют моменты затяжки критических резьбовых соединений, специальными приборами проверяется соответствие технических жидкостей в автомобиле.
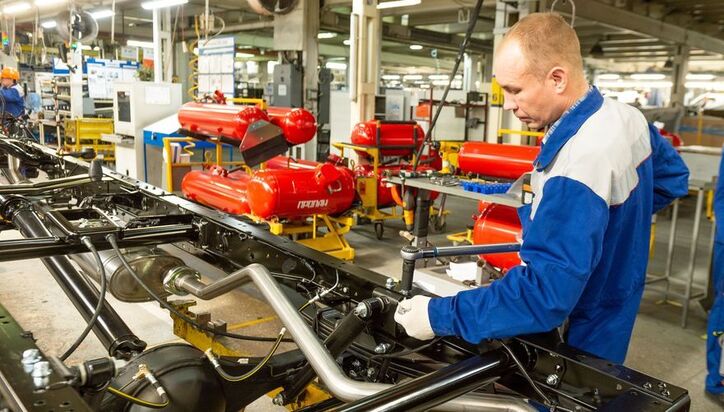
Анализ критических соединений, влияющих на безопасность водителей и пассажиров, ведут профессионалы своего дела.
- Крепление колес и подвески – одно из важнейших соединений в автомобиле и даже малейшее отклонение от нормы недопустимо, - рассказывает контролер Александр Будачев, отмечая, что применение электронных ключей гарантирует момент надежной затяжки. Информация о выполненной операции фиксируется в автоматическом режиме на инструменте и выведенных в отдельный стенд датчиках. По окончании операции она заносится в электронную базу, где хранится годами.
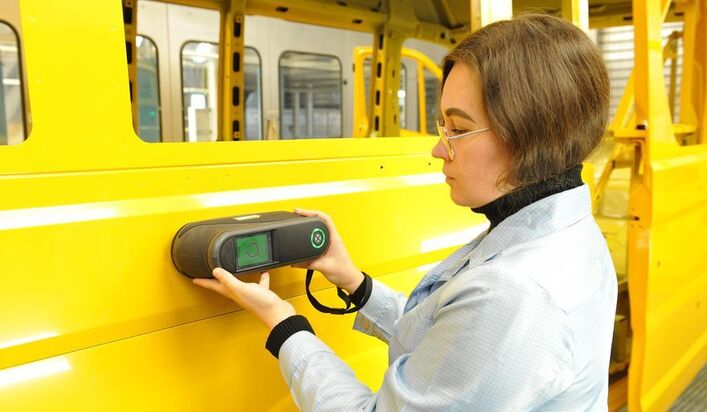
Среди новых инструментов контроля качества – курсирующие вдоль конвейеров инструментальные диагностические тележки, с помощью которых специалисты службы главного механика определяют возможность электронного ключа выдавать требуемые параметры.
По словам А.Будачева, в безупречном качестве выпускаемых автомобилей на автозаводе искренне заинтересованы все – начиная от слесарей механосборочных работ и заканчивая руководителями.
- Мы, контроллеры службы качества, находимся в постоянном контакте с бригадирами и лидерами групп. И на все замечания они всегда реагируют оперативно, - уточняет Александр.
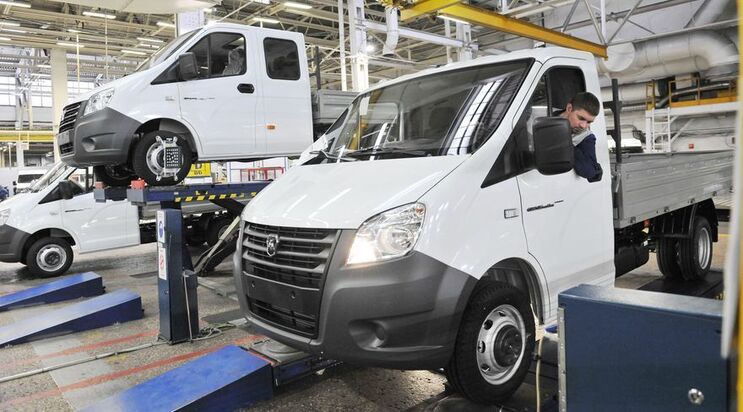
На службе качества в производстве - и цифровизация процессов. Например, в последние годы внедрена автоматизированная система, позволяющая блокировать дальнейшее оформление отгрузочных документов на автомобиль, если несоответствия по моменту затяжки не устранены.
Исключить малейшие погрешности сборки, тормозной, топливной системы, электрооборудования, посторонние шумы, установленных узлов и агрегатов, позволяет проверка готового автомобиля на современных испытательных стендах.
После обкатки на смотровой яме производится осмотр моторного отсека, шасси автомобиля на предмет наличия течей узлов и агрегатов. Далее следует регулировка света фар и развала-схождения колес, а затем новая машина отправляется на финальную станцию контроля собранного автомобиля, где окончательно проверяется экстерьер, интерьер кабины, кузова, грузовая платформа.
Следующий этап контроля качества сборки автомобиля - проверка на водонепроницаемость кузова и кабины. Она проводится в камере герметичности, где машина оказывается в условиях тропического ливня.
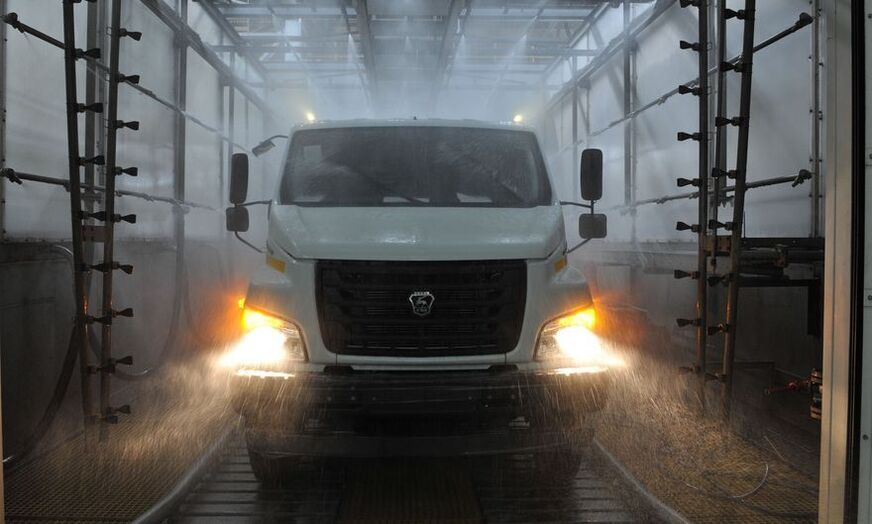
На финальной линии конвейера специалисты службы качества проверяют автомобиль в световом тоннеле, где он осматривается на предмет повреждений лакокрасочного покрытия. После этого автомобиль проходит процедуру приемки «с позиции потребителя» по качеству лицевой поверхности и механической части автомобиля. А перед самым выходом из проходной завода новая техника выборочно отправляется на испытательный трек, расположенный рядом с производством грузовых автомобилей.
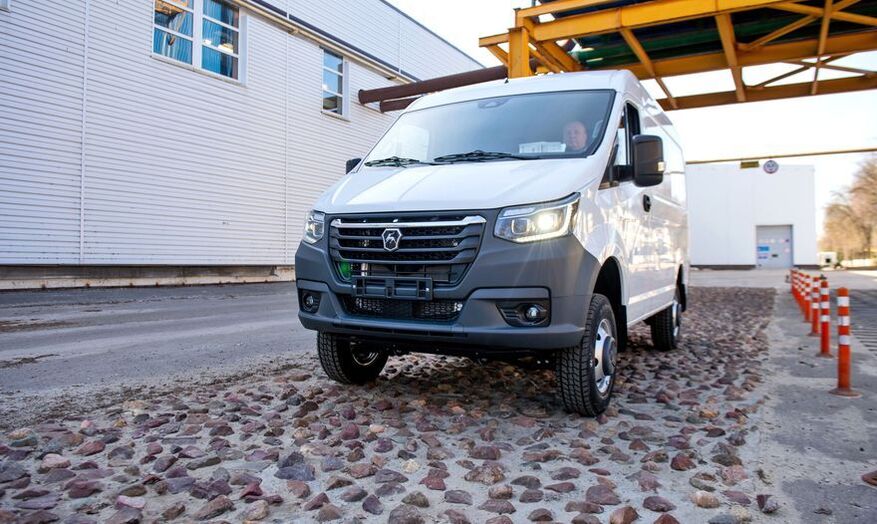
На этой трассе проверяется управление автомобилем и его устойчивость на 8 участках, включая «бельгийскую мостовую», «булыжник», «волну», резкий разгон и торможение на участке ровной дороги, затем идет проверка работоспособности электрических систем. Потом водитель-испытатель направляет машину на эстакаду, проверяя в деле ручной тормоз. В ходе такого многопланового маршрута всесторонне оценивается машина на ходу. Получив завершающий «ОК» от специалистов управления качества, автомобиль принимает статус: «Готов к отправке потребителю».
По материалам газеты «Автозаводец».